What Are the Different Types of 3D Printing Processes?
3D Printing is a relatively modern technology that allows for the layer-by-layer fabrication of physical models from computer aided design (CAD) files. It is a versatile process that has permeated virtually every industry.
Automotive manufacturers are using it to prototype designs and manufacture spare parts quickly, allowing them to innovate more frequently and reduce costs. In the aviation sector, it can help create lightweight parts that meet stringent aesthetic and structural requirements. Contact By3Design now!
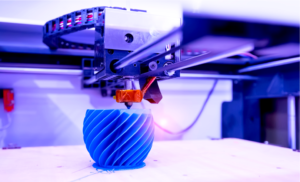
Fused deposition modeling is one of the most widely used 3D printing processes. It uses thermoplastic polymers and a layer-by-layer build process to create three-dimensional objects. The plastic is heated to its melting point through a hot nozzle and then deposited onto a build platform in thin layers. Each layer cools and solidifies before the next is deposited. This enables the printer to produce complex geometries that would be impossible or at least very expensive to make using traditional subtractive manufacturing methods.
FDM is often used in rapid prototyping, where prototypes are needed to test or present a new product design. It is also a good choice for concept and mockup models for presentations and design reviews. Its ease of use and affordable equipment price makes it a popular choice for smaller businesses.
Other applications include tooling, where FDM is used to create custom tools and parts to aid assembly and product operations. It can also be used to create jigs and fixtures for the manufacturing floor. Finally, FDM is sometimes used to produce functional components and custom implants for medical applications.
While FDM is a good choice for most of these applications, it is not the best for high-quality, smooth surfaces or for very fine features. Parts produced by FDM typically have a rough texture and may require additional post processing to remove surface blemishes. They are also less dimensionally accurate than those produced by other 3D printing technologies and may require support structures that need to be removed from the final part after printing. However, as the technology continues to improve and new materials become available, these issues will continue to be addressed.
2. Selective Laser Sintering (SLS)
SLS is a form of powder bed fusion that uses a high-power laser to heat and fuse small particles of polymer powder into a three-dimensional shape. It’s a great fit for users looking to print parts with complex geometry and precise shapes, allowing engineers to build prototypes that are both functional and aesthetically appealing.
In addition to its excellent dimensional accuracy, SLS printing offers several other benefits for both prototyping and end-use applications. Its ability to create intricate parts with undercuts and interlocking components allows for new design freedom that can reduce manufacturing costs, improve efficiency, and enhance part performance. SLS is also able to print metals such as titanium and aluminum through processes like DMLS and EBM, making it ideal for specialized industrial applications.
Another key benefit is that SLS prints are self-supporting, eliminating the need for time-consuming and resource-intensive post-processing procedures. This can significantly cut down the total cost of ownership and speed up time to market, enabling companies to bring products to life faster.
One limitation of SLS is that it can be limited by the range of materials available for use with this technology. The sintering process requires specific material properties, including an appropriate melting point and thermal stability. As a result, the selection of materials is more restrictive than for other 3D printing technologies, such as FDM and SLA.
SLS printers that utilize a cold metal fusion process, such as Nexa3D’s QLS230 and QLS236, have expanded the capabilities of this process even further. By combining fast cycle sintering with established powder metallurgy processes, these printers can produce titanium and steel parts directly from polymer-coated metal powders. For more information, visit our QLS230 and QLS236 pages.
3. Material Jetting
Material jetting is the AM process most like inkjet printing, depositing droplets of material to build parts layer-by-layer. This makes it one of the fastest technologies for producing prototypes and replacement parts. It also supports a broad range of materials, including standard polymers and even metals.
It can also print multiple colors, allowing designers to test and iterate their designs quickly without having to produce new molds. This design freedom also facilitates consolidation of several components into a single part, reducing assembly and maintenance time and costs.
This is a critical factor in the healthcare industry where medical devices can be printed based on each patient’s unique anatomy. From surgical tools to N95 masks, or a prosthetic designed for a specific individual, 3D printing has already made these and many other medical solutions available in much less time with the added benefit of lower cost and improved quality of life for patients.
The design freedom of 3D printing allows the creation of complex geometries that would be impossible or prohibitively expensive to manufacture using conventional methods. For example, the ability to create internal voids and lattices in parts can dramatically reduce weight without sacrificing strength. This is especially important for parts in high-performance applications, such as aerospace and automotive, where weight savings can have a significant impact on performance and fuel efficiency.
This capability, combined with the fact that 3D printing is a highly efficient manufacturing method, can significantly reduce operating and energy costs compared to traditional CNC machining. This is largely due to reduced cycle times and the avoidance of costly operations such as re-machine time, set-ups, and energy consumption. In addition, there is a significantly lower carrying cost for inventory and warehouse space. This translates into a rapid return on investment for any company that invests in a 3D printer.
4. Electron Beam Melting (EBM)
EBM is a metal 3D printing process that uses an electron beam to melt layers of metallic powder. The process takes place in a high-vacuum chamber filled with inert argon gas. The metal powder is spread across a build platform using rakes, then the electron beam from an electron gun is used to selectively melt and fuse parts of the layer according to slice data from a CAD model. Once the part is completed, excess powder is removed to reveal a solid metal end product.
Parts produced by EBM are durable, strong, and dense, making them suitable for functional prototyping and advanced manufacturing applications. They are also able to withstand high temperatures, which makes them well-suited for aerospace components and medical devices. In addition, the process can create complex geometries and specialized materials that are difficult to produce with other technologies.
Compared to SLM and binder jetting, EBM offers a higher level of accuracy with dimensions and tolerances typically within +-0.2 mm and fine features down to 0.3 mm. It also has a more uniform pore structure, which improves the mechanical properties of the finished product. The high levels of heat generated during the printing process also minimize residual stresses, resulting in a more stable part with superior strength and fatigue resistance.
Unlike other metal additive manufacturing processes, EBM produces minimal waste. Any unused powder can be gathered and reused, which reduces the costs of materials for subsequent prints. This can be a major cost savings in applications like the aerospace industry where machining can result in wasted material. In contrast, some other powder bed fusion technologies (such as SLM and LPBF) use up to 90% of the original powder in producing a single part.
5. Rapid Prototyping (RP)
The RP process offers significant design freedom, allowing designs to be modified easily, quickly and cheaply. This makes it possible to test and refine the design of a product in the early stages, potentially sidestepping errors that may be costly once production begins. This can reduce the time-to-market for a new product significantly and improve a company’s competitiveness.
RP can also enable the creation of complex geometric shapes that would not be possible or cost-effective using conventional machining. For example, RP can create components with internal cavities or voids to make the part lighter without compromising strength. This makes parts more functional and easier to use, especially in assembly and disassembly. It can also simplify maintenance and repair by keeping frequently replaced parts separate and accessible, making them easier to replace and less expensive.
A common use of RP is to make models for demonstration purposes. This can be in a variety of industries including architecture, manufacturing, medical, defence, automotive and energy. This is particularly useful when designing and presenting projects to clients or boards. It also helps to illustrate the real interrelationship of multiple components in a system.
In addition to its prototyping capabilities, RP can also be used for a wide variety of research and development activities. This includes sculpture, architecture, mold flow analysis, molecular modeling and an extensive range of other applications.
For many companies, RP can provide a cost-effective alternative to outsourcing to traditional contract manufacturers. It can reduce or eliminate tooling costs, minimum order quantities (MOQs), lead times/logistics and risk. In-house RP can also offer greater flexibility, enabling the company to respond rapidly to market change or customer demand.